Thermal Management in Electric and Hybrid Vehicles
- Marco Bonifaccino
- Jun 14, 2022
- 11 min read
Updated: Jun 15, 2022
The following information will give you an overview of the respective electric and hybrid technologies. From the basics and system properties, to solutions for thermal management and special features on the subject of maintenance, repair, and towing. You will also find important information about the qualifications required for the work in question.

Important safety information
The following technical information and practical tips have been compiled by AC diagnosis, source HELLA TECH WORLD, in order to provide professional support to vehicle workshops in their day-to-day work. The information provided on this blog is intended for use by suitably qualified personnel only.
HOW IMPORTANT ARE ELECTRIC AND HYBRID TECHNOLOGIES FOR THE WORKSHOP?
More than 2 million electric cars and plug-in hybrids were sold worldwide for the first time in 2018. With 2.1 million vehicles sold, their market share has risen to 2.4 percent of all new registrations – and the trend continues to rise. (Centre of Automotive Management). In Norway, for example, the market share is already at 50%!
According to the International Energy Agency (IEA), the growth of electric and hybrid mobility is driven primarily by government programs such as sales bonuses, local driving bans for cars with internal combustion engines, or targets for clean air. The authority considers e-vehicles to be one of several current drive technologies that can be used to achieve the long-term sustainability goals of reducing emissions. According to a study by management consultants PricewaterhouseCoopers,
every third new car registered in Europe in 2030 could be an electric car.
Therefore, it is no longer a question whether vehicles with electric, hybrid or hydrogen technologies will really prevail. They will soon become part of everyday life on our streets.
These vehicles will also have to be serviced and repaired, and the subject of thermal management will become increasingly complex.
The temperature control of the battery and power electronics plays just as important a role as the heating and cooling of the vehicle interior.
Air-conditioning components are also required for these types of drives – and their importance is increasing, since the air-conditioning system often has a direct or indirect influence on the cooling of the batteries and electronics. Air-conditioning maintenance will therefore play an even more important role in the future.
OVERVIEW OF HYBRID TECHNOLOGIES: COMPARISON
The term "hybrid" as such means a mix or a combination. With respect to vehicle engineering, this term means that an internal combustion engine with standard drive technology has been combined with elements of an electric vehicle in one vehicle.
Hybrid technology has three stages of complexity: from micro-hybrid to mild-hybrid up to full-hybrid technology. Despite technical differences, one thing all the technologies have in common is that the battery used is charged by recovering braking energy.
MICRO HYBRIDS
are usually equipped with a standard internal combustion engine, a start/stop automatic system, and a braking energy recovery (recuperation) system.
MILD HYBRIDS
in contrast also have an additional (small) electric motor and a more powerful battery. The electrical auxiliary drive is only used as assistance when starting and for greater power delivery when overtaking, a concept known as "boosting".
FULL HYBRIDS
can not only "boost"; they can also drive purely on electricity. To this end, they are fully equipped with an electric drive train. However, this requires a much more powerful battery than a mild hybrid.
PLUG-IN HYBRIDS
allow the batteries to be charged overnight, for example. The positive side effect of this vehicle type is that, at the same time, the passenger compartment can be brought to a desired temperature before the vehicle is driven. This means that the vehicle is immediately ready for use the following morning. The plug-in hybrid is a form of full hybrid.
HIGH-VOLTAGE SYSTEMS IN ELECTRIC VEHICLES: FUNCTION
By definition, an electric vehicle is a motor vehicle driven by an electric motor. The electrical energy required for its movement is obtained from a drive battery (accumulator), i.e. not from a fuel cell or a range extender. Since the electric car itself does not emit any relevant pollutants during operation, it is classified as an emission-free vehicle.
In electric vehicles, the wheels are driven by electric motors. Electrical energy is stored in accumulators in the form of one or more drive or supply batteries.
The electronically controlled electric motors can deliver their maximum torque even at standstill. Unlike internal combustion engines, they usually do not require a manual transmission and can accelerate strongly even at low speeds. Electric motors are quieter than petrol or diesel engines, almost vibration-free and emit no harmful exhaust emissions. Their efficiency of more than 90% is very high.
The relatively high weight of the accumulators is offset by the weight saving due to the elimination of the various components (engine, transmission, tank) of the combustion engine. Electric vehicles are therefore usually heavier than corresponding vehicles with combustion engines. The capacity of the battery(s) has a great influence on the vehicle weight and the price.
In the past, electric vehicles had short ranges with one battery charge. Recently, however, the number of electric cars that can reach distances of several hundred kilometres is increasing, for example: Tesla Model S, VW e-Golf, Smart electric drive, Nissan Leaf, Renault ZOE, BMW i3.
In order to further increase the range of electric vehicles, additional devices (usually in the form of an internal combustion engine) are sometimes used to generate electricity. This is referred to as the "range extender".
AIR CONDITIONING AND COOLING IN ELECTRIC VEHICLES
To be able to operate an electric vehicle with a particularly high level of efficiency, it is necessary to maintain an optimal temperature range for the electric motor, the power electronics and the battery.
This requires a sophisticated thermal management system:
- Refrigerant-based system (or direct battery cooling)
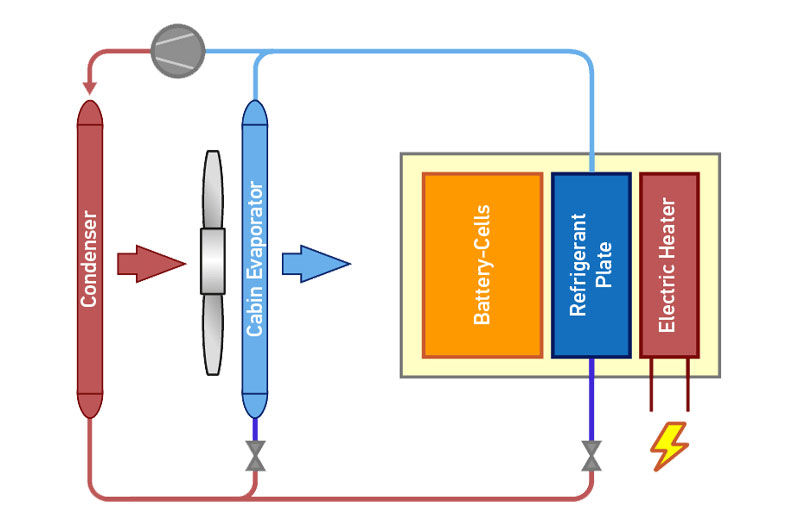
The circuit of the refrigerant-based system consists of the main components: Condenser, evaporator and battery unit (battery cells, cooling plate and electric auxiliary heater). It is supplied by the refrigerant circuit of the air-conditioning system and controlled separately via valves and temperature sensors. The functions of the individual components are described in the explanation for the illustration of the coolant and refrigerant-based system (b).
- Coolant and refrigerant-based circuit (or indirect battery cooling)
The more powerful the batteries are, the more the use of the comparatively complex coolant and refrigerant-based circuit makes sense.

The entire cooling system is subdivided into several circuits, each disposing of a separate cooler (low-temperature cooler), a coolant pump, thermostat and coolant stop valve. The refrigerant circuit of the air-conditioning system is also integrated via a special heat exchanger (chiller). A high-voltage coolant heater provides sufficient battery temperature control at low outside temperatures.
The coolant temperature for the electric motor and the power electronics is maintained at below 60 degrees Celsius inside a separate circuit (inner circuit on the figure) using a low-temperature cooler. For reaching full performance while ensuring the longest possible service life, it is necessary to always maintain the coolant temperature of the battery between approx. 15 and 30 degrees Celsius. When temperatures become too low, the coolant is heated via an auxiliary high-voltage heater. When temperatures become too high, it is cooled via a low-temperature cooler. Should this not suffice, a chiller integrated into both the coolant and refrigerant circuits, will further reduce the coolant temperature. Here, the refrigerant of the air-conditioning system flows through the chiller and further cools down the coolant, which also flows through the chiller. The entire control occurs via individual thermostats, sensors, pumps and valves.
INTERIOR AIR CONDITIONING: BASICS
In standard drive concepts with internal combustion engines, the air conditioning inside the vehicle directly depends on the engine operation due to the mechanically driven compressor. Compressors with belt drives are also used in vehicles that only have a start-stop function (referred to as micro hybrids by experts). The problem here is that when the vehicle is at a standstill and the engine is switched off, the temperature at the evaporator outlet of the air-conditioning system starts to increase after just 2 seconds. The associated slow rise in the temperature of the air blown in by the ventilation and the increase in humidity can be annoying for passengers.
In order to counter this problem, newly developed cold accumulators, so-called storage evaporators, can be used.
The storage evaporator comprises two blocks: an evaporator and an accumulator block. Refrigerant flows through both blocks in the start-up phase or when the engine is running. In the meantime, a latent medium in the evaporator is cooled so far that it freezes. This makes it a cold accumulator.
In the stop phase, the engine is switched off and the compressor is not driven as a result. The warm air flowing past the evaporator cools down and a heat exchange takes place. This exchange continues until the latent medium has completely melted. Once the vehicle continues on, the process starts again so that the storage evaporator can start cooling the air again after just one minute.
On vehicles that do not have a storage evaporator, the engine has to be started again even after a short standstill period in very warm weather. This is the only way to maintain interior cooling.
Air conditioning inside the vehicle also includes heating the passenger compartment if required. In full-hybrid vehicles, the internal combustion engine is switched off when driving using the electric motor. The prevailing residual heat in the water circuit is sufficient to heat the interior for a short period of time only. As support, high-voltage air auxiliary heaters are then switched on to take over the heating function. The operation is similar to that of a hair dryer: the air that is drawn in by the interior fan is heated up as it flows past the heating elements and then passes into the interior.
TEMPERATURE MANAGEMENT OF THE BATTERY: COMPARISON
The battery is essential for the operation of an electric and hybrid vehicle. It must provide the high amount of energy required for the drive quickly and reliably. Most of these are lithium-ion and nickel-metal hybrid high-voltage batteries. This further reduces the size and weight of the hybrid vehicle batteries.
It is imperative that the batteries that are used are operated within a defined temperature window.
Service life decreases at operating temperatures of +40 °C or higher, while efficiency drops and output is lower at temperatures below -10 °C.
Furthermore the temperature differential between the individual cells must not exceed a particular value.
Brief peak loads in connection with high current flows, such as from recuperation and boosting, lead to a significant increase in the temperature of the cells. Also, high outside temperatures in the summer months can mean that the temperature quickly reaches the critical 40 °C level.
When the temperature is exceeded, the result is faster aging and the associated premature failure of the battery. Vehicle manufacturers strive to ensure that the calculated battery lifetime is 1 car life (approx. 8-10 years). Therefore, the aging process can only be countered with a corresponding temperature management system.
Until now, three different temperature management options have been used.
- Option 1
Air is drawn in from the air-conditioned vehicle interior and is used to cool the battery. The cool air drawn in from the vehicle interior has a temperature of less than 40 °C. This air circulates around the accessible surfaces of the battery pack.
Disadvantages of this are:
Low cooling effectiveness.
The air suctioned from the vehicle interior cannot be used to reduce the temperature evenly.
Considerable effort required to guide the air.
Possibly annoying noises in the vehicle interior caused by the blower.
There is a direct connection between the passenger compartment and battery via air ducts. For safety reasons (e.g. outgassing of the battery) this is problematic.
Another factor that should not be underestimated is the risk of dirt entering the battery pack because the air from the interior of the vehicle also contains dust. The dust is deposited between the cells and forms a conductive layer together with condensed humidity. This layer facilitates the creation of leak currents in the battery.
To avoid this risk, the intake air is filtered. Alternatively, air cooling can also be effected by a separate small air-conditioning unit similar to the separate rear air-conditioning systems in luxury-class vehicles.
- Option 2
A special evaporator plate inside the battery cell is connected to the air-conditioning system in the vehicle. This is done using what is known as the splitting process on the high-pressure and low-pressure side via pipelines and an expansion valve. This means that the evaporator inside the vehicle and the evaporator plate in the battery, which works like a normal evaporator, are connected to the same circuit.
The different tasks for the two evaporators result in different requirements for refrigerant flow accordingly. While the interior cooling system aims to satisfy the comfort demands of the passengers, the high-voltage battery must be cooled to varying degrees of intensity depending on the driving situation and the ambient temperature.
These requirements are the defining factors for the complex control of the quantity of evaporated refrigerant. The special design of the evaporator plate and its resulting integration into the battery offer a large contact surface for the heat exchange. This means it is possible to guarantee that the critical maximum temperature of 40 °C is not exceeded.
When the outside temperatures are very low, increasing the battery temperature to the ideal temperature of the battery may require an increase of at least 15 °C. However, the evaporator plate cannot help in this situation. A cold battery is less powerful than one that has the right temperature. It is also difficult to charge the battery when temperatures are significantly below freezing. In a mild hybrid, this can be tolerated: in extreme cases, the hybrid function is only available in a limited capacity. It is, however, still possible to drive with the internal combustion engine. On the other hand, a battery heater needs to be fitted in purely electric vehicles so that the vehicle can be started and driven whatever the situation in the winter.
Note
Evaporator plates that are directly integrated into the battery cannot be individually replaced. Therefore, the whole battery needs to be exchanged in the event of damage.
- Option 3
The correct temperature plays a key role for batteries with higher capacities. Therefore, an additional battery heater is required at very low temperatures to ensure the ideal temperature range is achieved. This is the only way to achieve satisfactory range when in the "electric driving" mode.
To enable this additional heating, the battery is integrated into a secondary circuit. This circuit ensures that the ideal operating temperature of 15 °C – 30 °C is maintained at all times.
Coolant, made of water and glycol (green circuit), flows through a cooling plate integrated into the battery block. At lower temperatures, the coolant can be quickly heated by a heater in order to reach the ideal temperature. The heater is switched off if the temperature in the battery rises when the hybrid functions are being used. The coolant can then be cooled via a battery cooler located in the vehicle front end or low-temperature cooler using the airstream from the vehicle driving forward.
If the cooling by the battery cooler is not sufficient at high outside temperatures, the coolant flows through a special heat exchanger. In it, refrigerant from the vehicle air-conditioning system is evaporated. In addition, heat can be transferred from the secondary circuit to the evaporating refrigerant in a very compact space and with a high power density. An additional re-cooling of the coolant is performed. Thanks to the use of the special heat exchanger, the battery can be operated within the most efficient temperature window.
BASIC RULES FOR WORKING ON ELECTRIC AND HYBRID VEHICLES: PRACTICAL TIPS
Electric and hybrid vehicles necessitate the installation of high-voltage components. These are clearly identified with uniform warning signs. Also, all manufacturers mark high-voltage lines with a bright orange colour.
The following procedure applies when working on vehicles with high-voltage systems:
Completely switch off the electrical system
Secure against current being switched on again
Check there is no voltage present
What do I have to pay attention to as a workshop (employee)?
Starting and moving the vehicle: In order to drive a vehicle with a high-voltage system – even if only from or to the workshop – the respective person must be instructed
Service and maintenance: Service and maintenance work (changing wheels, inspection work) on high-voltage vehicles may only be carried out by persons who have previously been informed of the dangers of these high-voltage systems and instructed accordingly by a "Fachkundiger für Arbeiten an HV eigensicheren Fahrzeugen" (expert for work on HV intrinsically safe vehicles)
Replacement of high-voltage components: Persons replacing high-voltage components such as an air-conditioning compressor must have the appropriate qualifications ("expert for work on HV intrinsically safe vehicles")
Replacing the battery: The repair or replacement of live high-voltage components (batteries) requires special qualification.
Roadside assistance/towing/recovery: Anyone providing breakdown assistance on vehicles with high-voltage systems or towing or recovering them must have received instruction in the structure and functioning of the vehicles and their high-voltage systems. Furthermore, the respective instructions of the vehicle manufacturer must be taken into account in advance. If high-voltage components (battery) are damaged, the fire brigade should be consulted
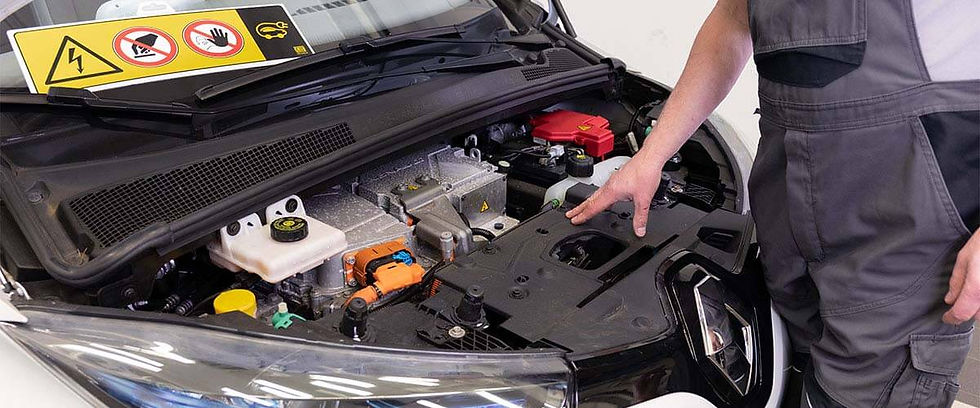
How do I recognize that the vehicle has a high-voltage system?
By the lettering on the dashboard or on the vehicle
By orange high-voltage cables (see illustration). As a general rule: hands off high-voltage components and orange cables
By the marking on the HV components (see illustration)
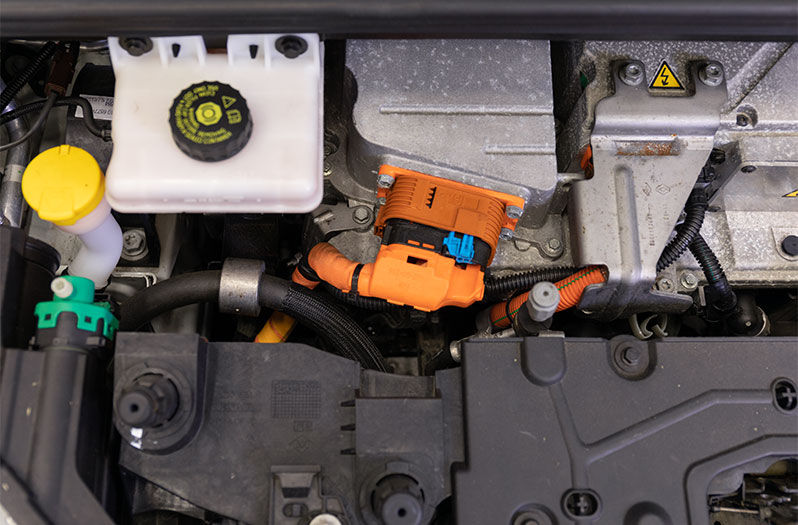
Source: HELLA TECH WORLD
Comentários